In many industrial environments, cleanliness is judged by what we can see. But in advanced industries with critical environments, control starts far earlier – before any dust settles or surface is wiped. At scale, the difference between spotless and stable is vast.
Cleaning addresses symptoms. Contamination control tackles the root cause.
Cleaning vs. Contamination Control
In battery manufacturing, traditional cleaning is a familiar routine. Floors are mopped, surfaces wiped down, and “black dust” is removed from equipment using solvents, sweepers, or wipes. These actions create a sense of order, but only temporarily.
Cleaning is reactive by nature. It takes place after contaminants have already entered the environment, usually in response to visible buildup. While sometimes necessary, cleaning alone is a short-term intervention. Over time, it introduces hidden costs — halting production, increasing exposure risk, and contributing to material waste.
In dry room environments, those risks are amplified. Surfaces that appear clean may still hold fine metal dusts, including nickel, cobalt, and lithium. Wiping them without proper containment can reintroduce hazardous particles into the air — increasing exposure and undoing previous efforts.
Without preventive systems in place, each sweep risks becoming a cycle — removing some particles, disturbing others, and redistributing contaminants along the way.
Contamination control takes a different approach. Rather than reacting to what has already happened, it prevents contaminants from being introduced or spreading in the first place. It is a strategic design principle, not a maintenance task.
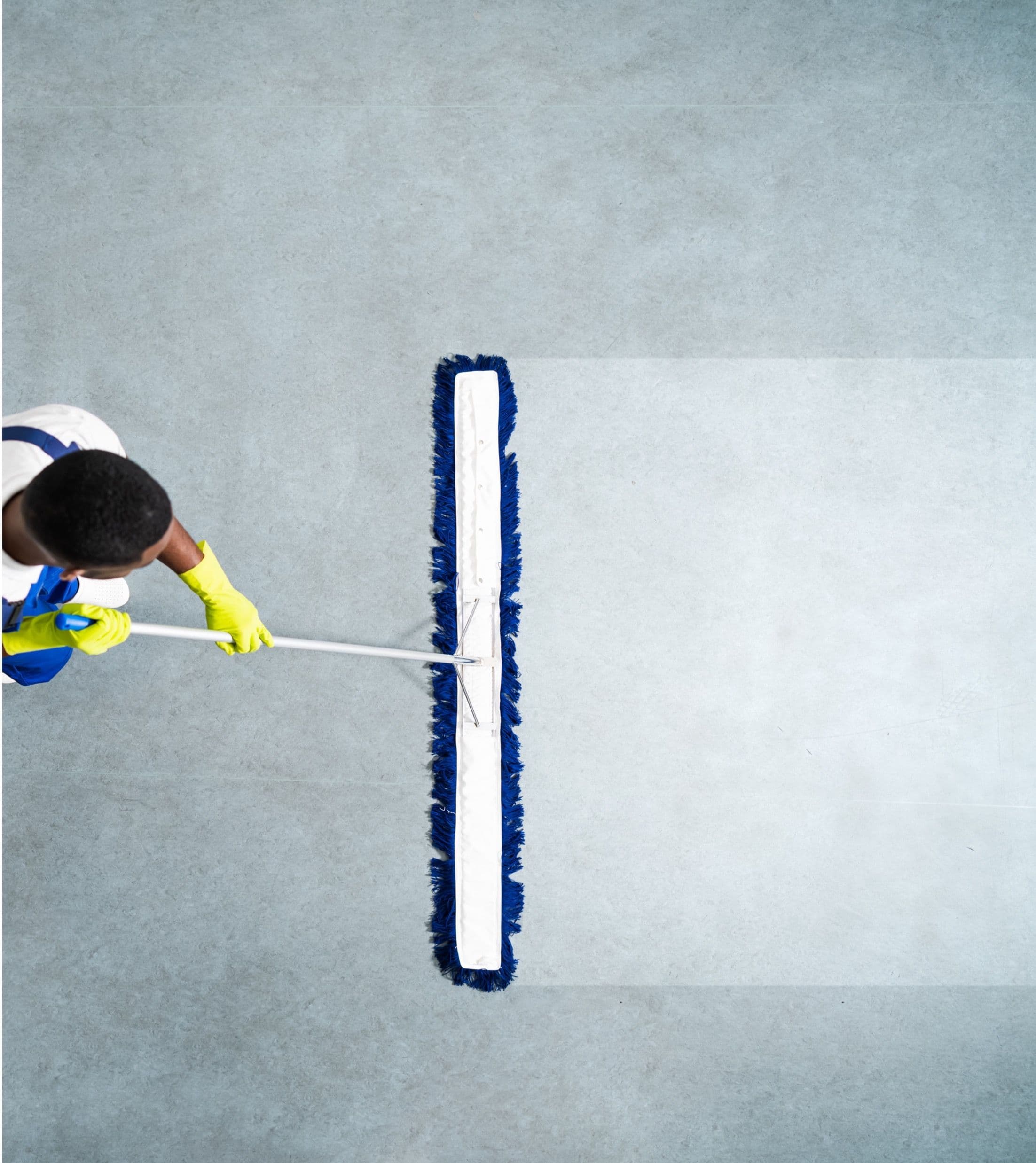
Cleaning – Shutterstock
What is Contamination Control?
Contamination control is best understood as an immune system for advanced manufacturing. It doesn’t simply respond to threats — it anticipates them. Embedded into the architecture, routines, and behaviors of high-stakes environments, it works continuously and quietly to safeguard against risks that are often invisible to the naked eye.
At its core, contamination control refers to a coordinated set of practices and systems designed to prevent, detect, and eliminate foreign particles or substances that could compromise safety, product quality, or operational integrity.
It’s essential in industries where precision is a baseline requirement:
- Pharmaceuticals, where sterility preserves both health and efficacy.
- Semiconductors, where a single airborne speck can cause circuitry failure.
- Battery manufacturing, where safety, performance, and sustainability converge at the particulate level.
In each of these sectors, the tolerance for error is small. That’s why contamination control spans the full production lifecycle and defines what is and isn’t allowed to enter.
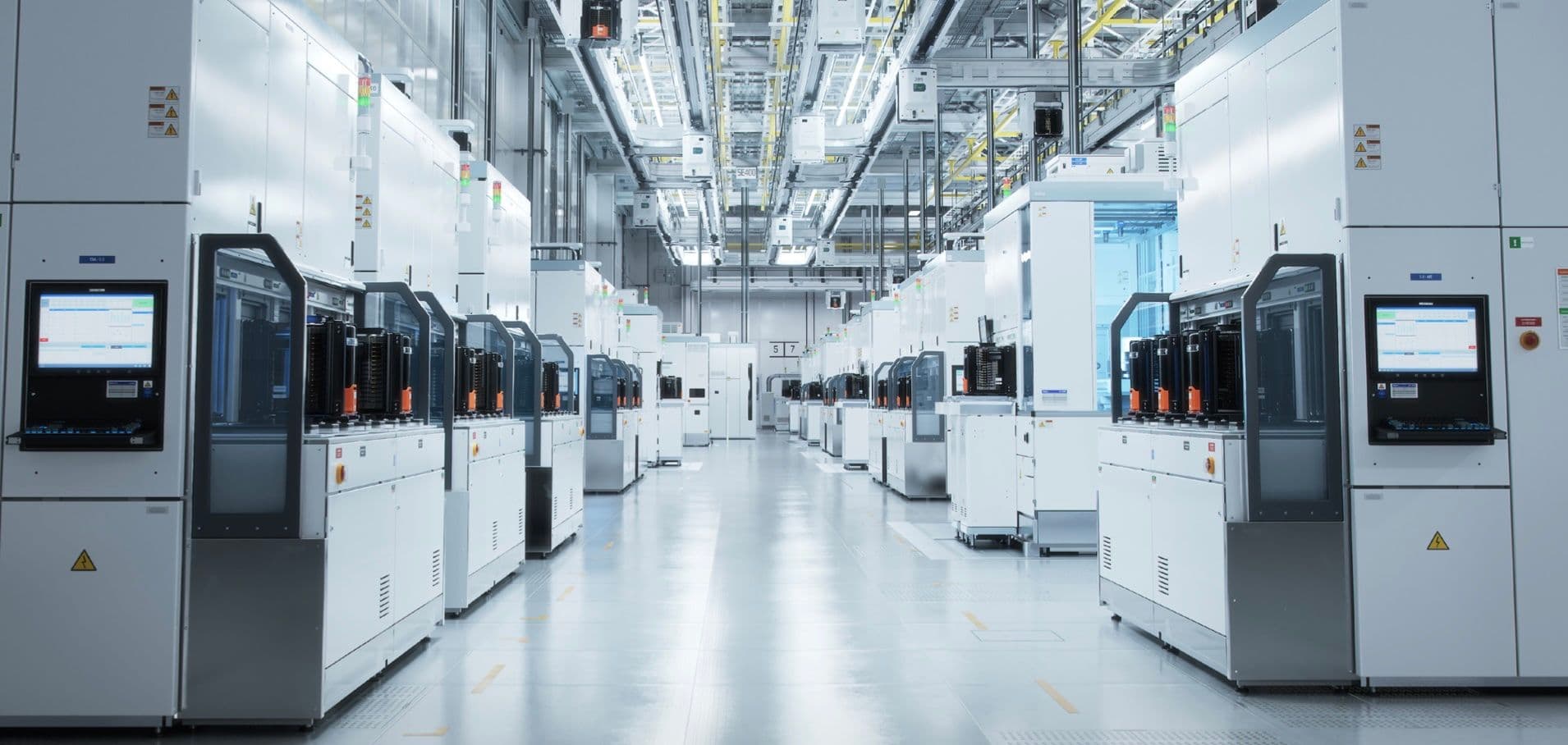
Cleanroom – Adobe Stock
Understanding the Contaminants
Contamination in battery manufacturing doesn’t announce itself. It enters quietly — carried in by the routines that keep production moving. What appears clean may, in reality, be a complex network of invisible threats.
Contaminants typically enter through five primary pathways:
- People
Human presence is the most consistent source. Particles from skin, hair, and clothing fibers become airborne through minor movements. Even with protective gowning and protocols, these particles can travel through airflow systems and settle in production zones. - Air Systems
Ventilation, if improperly balanced, can draw particles between rooms. In dry rooms, where air is recirculated and humidity is low, particles remain suspended longer, raising the stakes for air handling performance. - Materials and Packaging
Even materials that pass inspection can carry trace contaminants. Pallets, packaging, or raw inputs may introduce dust or chemical residues from earlier stages, especially when handled in less controlled settings. - Manufacturing Processes
Processes like cutting, grinding, or friction release fine metal and carbon dust — often electrostatically charged, making them difficult to contain and likely to migrate. - Equipment
Unmaintained tools and machinery can shed debris or leak residues. Even automated systems can introduce contamination through wear, lubrication breakdown, or unnoticed faults.
The most dangerous particles are often the ones we can't see."
Dr. Christina Isaxon
Associate Professor, Lund University
But these particles don’t only compromise products and processes, they also affect the people working in these environments. As Dr. Christina Isaxon shared in our recent interview, contaminants like nickel, cobalt, and lithium can become airborne during manufacturing, exposing employees to substances that may pose long-term health risks.
While cleanrooms and decontamination routines are often designed to protect the product, they’re not always designed with people in mind. That’s why isolating workers from hazards, through engineering controls that manage contaminants at the source, is essential to crating a clean and safe environment.
Designing for Control – Good Manufacturing Practice
A robust contamination control strategy is not built on equipment alone. It is embedded in the architecture of a facility, the logic of its layout, and the habits of its people. The most resilient systems weave together design, behavior, and monitoring into one coordinated framework: Good Manufacturing Practice (GMP).
Regulatory frameworks such as EU GMP Annex 1 and FDA Guidance for Industry treat contamination control as a pillar of manufacturing quality for the pharmaceutical industry. As battery production scales and tolerances tighten, that guidance will become essential.
To build resilience from the ground up, contamination control spans multiple layers:
- Cleanroom classification – ISO-rated rooms with pressure-controlled zones filter and direct airflow.
- Filtration systems – HEPA and ULPA filters remove particulates with high efficiency.
- Environmental monitoring – Air quality, temperature, humidity, and particles are tracked in real time.
- Standard Operating Procedures – Protocols govern gowning, tool use, and material flows.
- Zoned facility design – Physical separation of raw materials, personnel, and finished goods minimizes cross-contamination.
- Sensor-based alerts – Early warnings allow for quick action when thresholds are exceeded.
And these layers aren’t static. They evolve alongside the materials, processes, and risks they’re designed to protect.
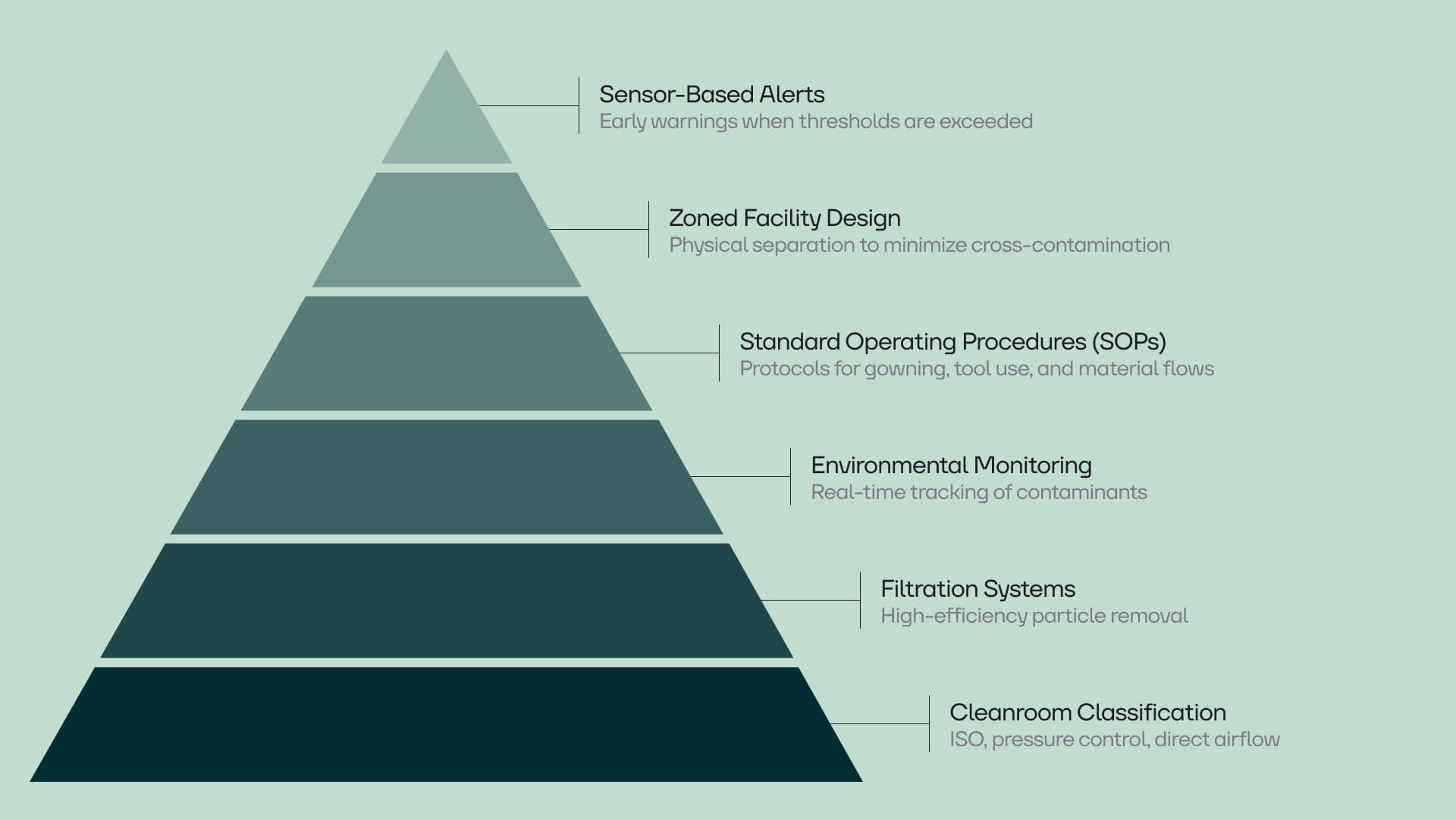
What Other Sectors Can Teach Us
The battery industry doesn’t need to start from scratch. Other sectors have already built robust models of contamination control:
- Pharmaceuticals bring decades of experience in zoning, hygiene, and behavioral protocols — prioritizing health and safety.
- Semiconductors offer leadership in static control, airflow modeling, and traceable particle tracking — where the margin for error is microscopic.
Together, they show that contamination control is not a cost center. It is a quality system and a foundation for long-term resilience. As battery manufacturing advances, these cross-sector learnings can help bridge the gap between short-term solutions and structural excellence.